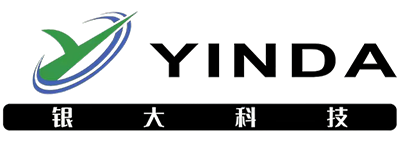
[encyclopedia] powder spraying is to spray powder coating to the surface of workpiece by powder spraying equipment (electrostatic spraying machine). Under static electricity, powder will be evenly adsorbed on the surface of the workpiece to form a powder coating; the powder coating is solidified by high temperature baking and leveling, and becomes the final coating with different effects (different kinds of effect of powder coating); the spraying effect of powder spraying is in the machine The strength, adhesion, corrosion resistance and aging resistance of the machine are superior to the painting process, and the cost is also under the same effect of painting.
Electrostatic powder coating technology of building aluminum profile is a surface treatment technology which is rapidly rising in recent years. It has the characteristics of no solvent, no pollution to the environment, and the powder can be recycled, easy to realize automatic production, easy to use, and the coating color is diverse and can meet the requirements of different weather resistance. However, some defects often appear in electrostatic powder spraying of aluminum profile, which affect the appearance quality and performance of the products.
The causes of common coating defects and control measures are briefly described below:
1、 Defect Name: particle
Cause analysis: the surface of the base material has burr, aluminum chip and graphite mark, and the pretreatment is not good; the residue of the pretreatment tank liquid adheres to the profile surface, and the water washing is not clean in place; the chrome material is placed for a long time and the surface is adsorbed with dust; the new burning fixture is not used properly, which causes the surface of chromium to fall off; the powder and the recovery powder may contain impurities; the spraying site and curing furnace are not clean and suspended Things.
Control measures: grind the surface of blank or sandblasting before upper row to ensure that the pre-treatment is in place; regularly pour the groove to clean the residue and extend the time of pure water washing; carefully blow dust after the chrome material is discharged; spray a thin coating on the new burning fixture and use it after passing the screen; the workshop shall be under 6S management, keep the spray site clean and clean the curing furnace regularly.
2、 Defect Name: exposed bottom
Cause analysis: the coverage of powder coating is poor; the profile section structure is complex and easy to cause electrostatic shielding effect; the hanging method is improper; the responsibility of the spray room worker is not strong, the business ability is poor, the thickness of the powder film is not judged properly; the powder deposition at the nozzle is too much, and the blockage; the gun moves too fast or the chain speed is too fast; the profile decoration surface is not clear.
Control measures: strictly control the quality of powder coating; manually supplement the profile groove and inner corner; adjust the angle of profile hanging; improve the skills of the spraying room worker; the spray room worker shall try to measure the thickness of the profile film after curing as soon as possible; clean the nozzle mouth regularly to keep it smooth; adjust the speed of the gun movement to reduce the chain speed properly; understand the requirements of the customer spraying and recognize the decorative surface of the profile.
3、 Defect Name: uneven coating
Cause analysis: the hanging mode and arrangement of chrome materials are not correct; the profile is poorly grounded (poor electrical conductivity of individual hanging tools); the conveying chain speed is not uniform, or the chain speed is not in line with the rising and descending speed of the spray gun, and the powder coverage times of profile decoration surface are not consistent; the powder output and powder atomization of the spray gun are not appropriate; the compressed air pressure is unstable; the voltage of the high electrostatic generator is unstable and the static voltage changes.
Control measures: strengthen the communication between the upper row workers and the spray room workers, and select the corresponding hanging tools for profile; check whether the hanging tools are conductive; the spraying room workers shall strengthen the function improvement, and coordinate the hanging density, chain speed and lifting speed during spraying; control the ratio of powder gas and powder gas; strengthen equipment maintenance and maintain the stable operation of the equipment.
4、 Defect Name: variegation
Cause analysis: when the spraying room is cleaned by changing colors, the cleaning is not thorough enough and the powder is infiltrated to cause the miscellaneous color; the powder (recycled powder) is not baked timely to correct the color; the surrounding environment of the spray room is not clean.
Control measures: when cleaning the spray room, the spray room worker shall carefully clean every detail, especially the powder pipe of spray gun, and the cyclone shall be carefully blown clean. After cleaning the spray room, the baking plate must be roasted to confirm whether there is any impurity; after the baking board is confirmed to be qualified, the surrounding of the spray room shall be kept clean at any time.
5、 Defect Name: shrinkage hole
Cause analysis: the pretreatment degreasing is not complete; the compressed air quality is unqualified, and the powder supply gas and atomizing gas contain oil content; the chrome material may be polluted by oil and water stains during the circulation; the oil pan under the chain is deformed, causing the oil drop pollution of the chain; the resin is incompatible and the shrinkage caused by mixing powder.
Control measures: adjust degreasing process to ensure the profile oil removal is clean; carefully check the surface quality of chrome material, prevent oil and water pollution when storing and circulating chrome; check the quality of compressed air and operation of water removal and oil removal equipment, timely discharge condensed water and oil of compressed air; check the use of chain lubricating oil to avoid pollution; use fine cleaning mode to change color and clean it Blow clean the powder pipe and powder spraying system.
6、 Defect Name: coarse sand
Cause analysis: coarse sand refers to the rough surface of sand grain powder coating, the main reasons are: discharge at the edge or tip of profile during electrostatic spraying, high voltage; the distance between spray gun and profile is small, and the electric field strength is too large; poor electrical conductivity of hanging tools leads to poor powder loading or heavy reverse ionization; poor powder quality causes coarseness of coating after curing.
Control measures: strictly control static voltage, distance between spray gun and profile, and implement powder spraying process requirements; before hanging, joints between hanging tool, chain and profile shall be fully polished to ensure good conductivity; and the quality of powder coating shall be strictly controlled.
7、 Defect Name: color difference
Cause analysis: the color difference is caused by the uneven powder pigment; different batches of powder coating; the curing temperature and time are different; the coating film thickness is uneven.
Control measures: strengthen the quality control of powder; inspect the powder coating in different batches and put new powder into the baking plate; keep the same curing temperature and time of the same batch of spray profile, and fix the aluminum coating on the production line for special powder; strengthen the powder spraying process control to avoid the excessive gap of coating film thickness.
8、 Defect Name: coating scratch
Cause analysis: before the spraying finished products are discharged, turned around and coated, the decorative surface of spray coating is scratched due to friction between long and short materials or improper manual operation.
Control measures: the lower row of spray products shall be placed according to different length; workers shall coordinate with each other when handling the profile, so as to handle them lightly.
9、 Defect Name: powder discharge
Cause analysis: the fluidization effect of powder is poor due to moisture and agglomeration, and the powder concentration in the powder conveying pipe is uneven; the fluidizing plate is blocked by powder, and the fluidization effect of the powder supply device is poor; the powder pipe, powder pump, Wenqiu pipe, electrostatic needle, spray gun nozzle and other accessories are seriously damaged, resulting in uneven powder output and powder discharge.
Control measures: improve the storage environment of powder, seal the powder box timely after use to avoid the powder from moisture; do well the maintenance of powder supply equipment; clean the powder scale on the equipment accessories of spray room in time and replace the wear parts.
In the actual powder spraying production, every process must be carefully managed. The coating defects should be treated to the right point, and similar coating defects should be avoided as much as possible, so as to reduce the production cost and improve the quality of powder coating.
Source: Aluminum Friends Community