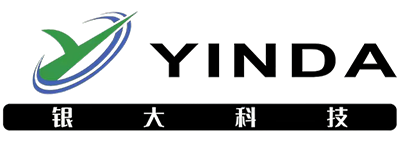
The color of spraying profiles is various, which is popular with customers. However, due to the complexity of section shape of aluminum profiles, it is difficult to spray production and coating thickness inspection. No matter what the shape of the aluminum profile is, the minimum local film thickness of the coating on the surface of the aluminum profile is not less than 40um, which is a mandatory implementation clause specified in gb5237.4-2008 and must be strictly observed; others, such as the inner corner, transverse groove and groove, are not allowed to have enough film thickness, but cannot be exposed.
In the actual production, due to the influence of electrostatic spraying equipment and aluminum profile section shape, the accurate control of coating thickness is a must. The characteristics of spraying production line can better control the coating thickness from the following aspects.
1. Hanging mode
The key to control coating thickness is to select proper hanger according to the shape of aluminum profile and correct hanging method. It can not only improve the coating quality of aluminum profile, but also reduce the workload of manual powder mending by powder room operators. In particular, the thickness of powder coating can be adjusted according to the hanging spacing. The general requirement of hanging spacing is: width of aluminum profile = spacing of aluminum profile .
2. The workpiece is in contact with the hanger
Due to the poor contact between the workpiece and the hanger (i.e. poor conductivity), the coating efficiency and coating quality will be seriously affected, resulting in the phenomenon of low coating film thickness and even bottom exposure due to the low powder loading rate of the workpiece, and causing great pressure on the recovery system, so that the excess powder will float out of the powder room before it can be recovered, which not only reduces the utilization rate of powder, but also pollutes the environment.
When the workpiece is in poor contact, the coating thickness measured at different points on the same material may vary from 30um to 70UM. In some places, because the coating is too thick, there will be orange peel, pinhole, flow mark and other defects, and the color and gloss will also be affected. In addition, the obvious zebra like defects of sand grain powder profile can be detected visually under natural light. Therefore, it is necessary to ensure the good conductivity between the workpiece and the hanger.
3. Conveyor chain speed and production process
In production, the speed of the conveying chain and the production process play a major role in the thickness of the powder spraying coating, such as the lift stroke, gun distance, powder pressure, electrostatic voltage, etc. the general requirements for the lift stroke height are: stroke height = workpiece height + 200 mm. The more complex the shape of the workpiece is, the closer the distance between the spray gun and the workpiece is, the smaller the powder output is required and the lower the voltage is; on the contrary, the simpler the shape of the workpiece is, the farther the distance between the spray gun and the workpiece is, the larger the powder output is and the higher the voltage is.
4. Powder filling method of hand spray gun
Due to the complexity of the cross-section shape of aluminum profile, in the production process, as the inner corner of the decorative surface, the transverse groove and groove are not easy to be sprayed by the automatic spray gun, so the manual spray gun must be used for supplementary spraying. When the nozzle of the manual spray gun is facing the place to be sprayed on the workpiece, the transmission pressure adjustment is too large, and the distance between the manual spray gun and the workpiece is too close, it is easy to cause orange peel and flow marks on the surface of the workpiece , pinholes, gun punches, fat edges, etc. Generally, when the nozzle of the hand gun is facing the place to be sprayed on the workpiece, the transmission pressure is 1.2 ~ 1.8bar, and the distance between the hand gun and the workpiece should be controlled at 80 ~ 150mm.
5. Powder pump factors
In the production process, the common uneven powder discharge is mainly caused by the uncleanness of the venturi powder pump. Because the powder pump tightly presses the powder suction pipe, it is easy to produce powder accumulation and sticking, which will cause blockage. As a result, the receiving force in the powder pipe will be affected, thus affecting the coating thickness of the workpiece. Generally, the powder room operator should check the cleanliness of each part of the venturi powder pump in time.